Co-Packing for E-commerce: Meeting the Challenges of Online Retail
Online retail is a game-changer in the business world, particularly in the frozen food industry. With e-commerce, suppliers can now reach a global customer base, and consumers can easily shop for products in the comfort of their own homes. However, with the increasing demand of online shopping, challenges have arisen, particularly in the area of co-packing. Co-packing involves a supplier outsourcing the packaging and assembly of their products to a third-party co-packer.
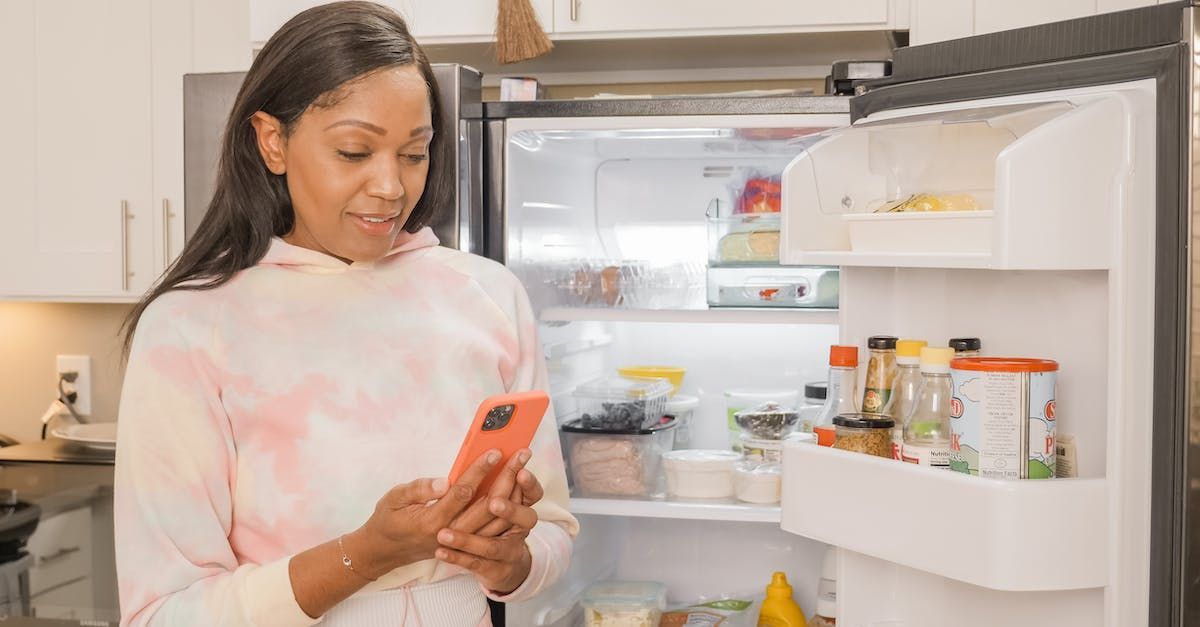
In this blog, we will explore the challenges of co-packing for e-commerce and how to mitigate them.
Supply Chain Challenges:
The supply chain is an essential aspect of co-packing, and e-commerce introduces a whole new set of challenges to this process. Firstly, the unpredictable nature of online orders, which could range from only a few items to hundreds, can create inventory and stocking issues. Secondly, timely delivery of products is critical in online retail, and any delays can lead to negative customer reviews, affecting a company's reputation.
Packaging and Shipping Regulations:
E-commerce regulations, such as the dimensional weight pricing system for shipping, are different from those of traditional retail. Packaging also needs to be up to standard to survive the transportation process. Using the wrong type of packing material or not meeting the weight and size requirements can result in extra charges and lost products.
Quality Control:
Co-packers are responsible for assembling and packaging the products based on the supplier's specifications. Therefore quality control measures must be in place to ensure the products meet or exceed customer expectations. This can be challenging as products may have unique assembly instructions and quality control requirements.
Communication:
Open and effective communication between suppliers and co-packers is essential for co-packing success. Communication helps to ensure that all parties understand individual responsibilities, timelines, and expectations. Communication should commence well before production begins so that there's ample time to iron out any differences.
Cost:
The cost of co-packing for e-commerce can be higher than that of traditional retail. This is due to requirements such as specialized packaging and shipping methods, additional quality control measures, and inventory holding expenses. Mitigation strategies may include adopting a just-in-time (JIT) inventory system, using more efficient packaging materials, and optimizing transportation routes.
In summary, co-packing for e-commerce comes with its unique challenges. As a supplier, it's essential to work with a co-packer that understands the intricacies of e-commerce. Effective communication, an efficient supply chain, attention to packaging and shipping regulations, quality control measures, and cost optimization strategies will go a long way in mitigating these challenges. With a good co-packing partner, you can reap the benefits of e-commerce without having to worry about its challenges.

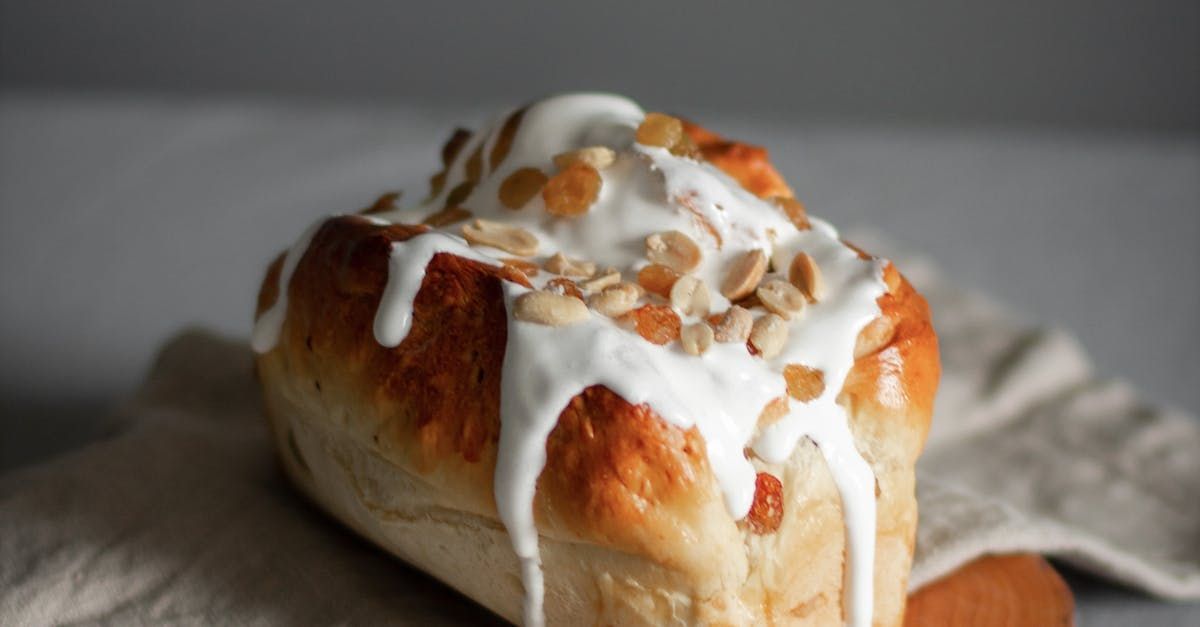
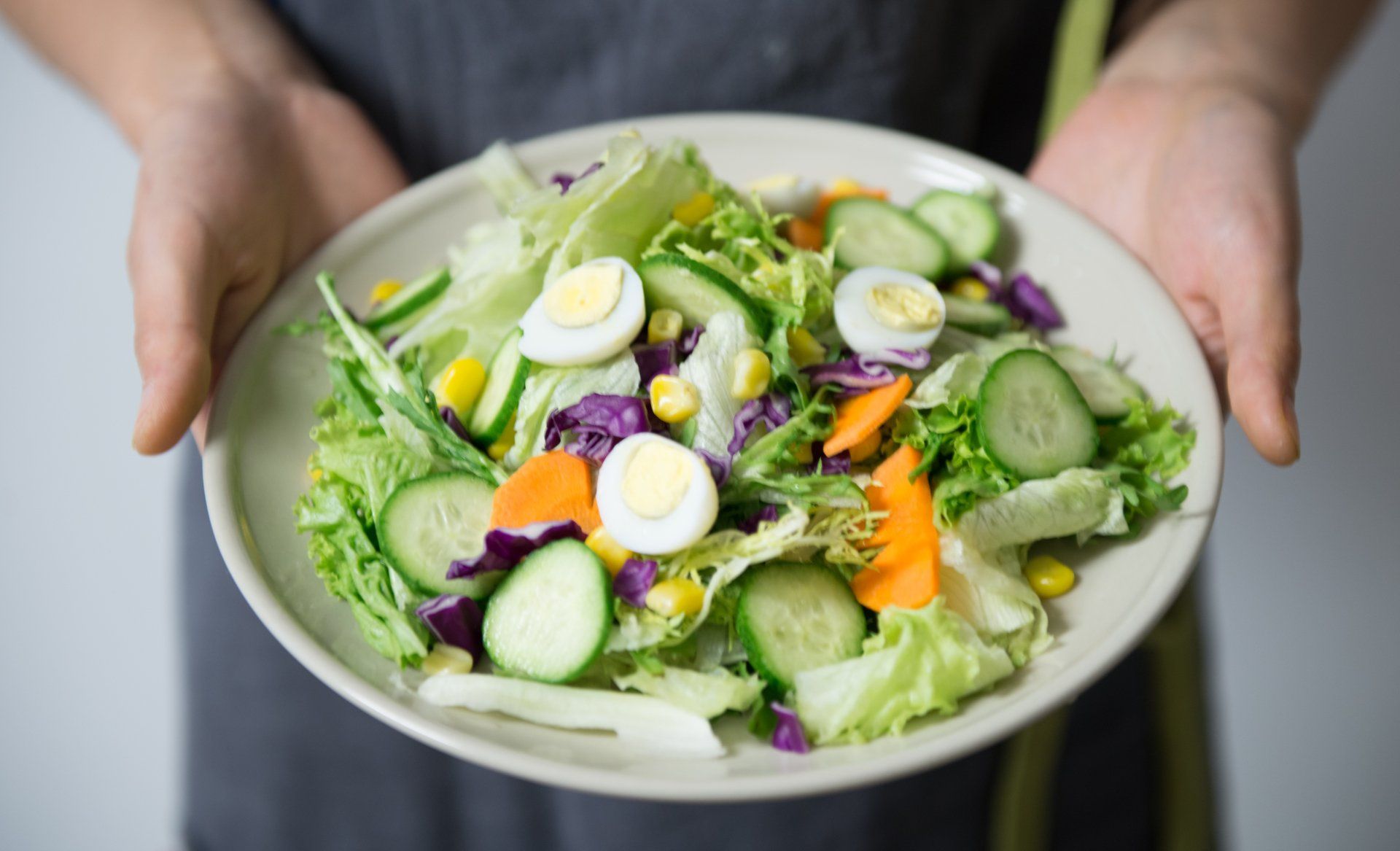
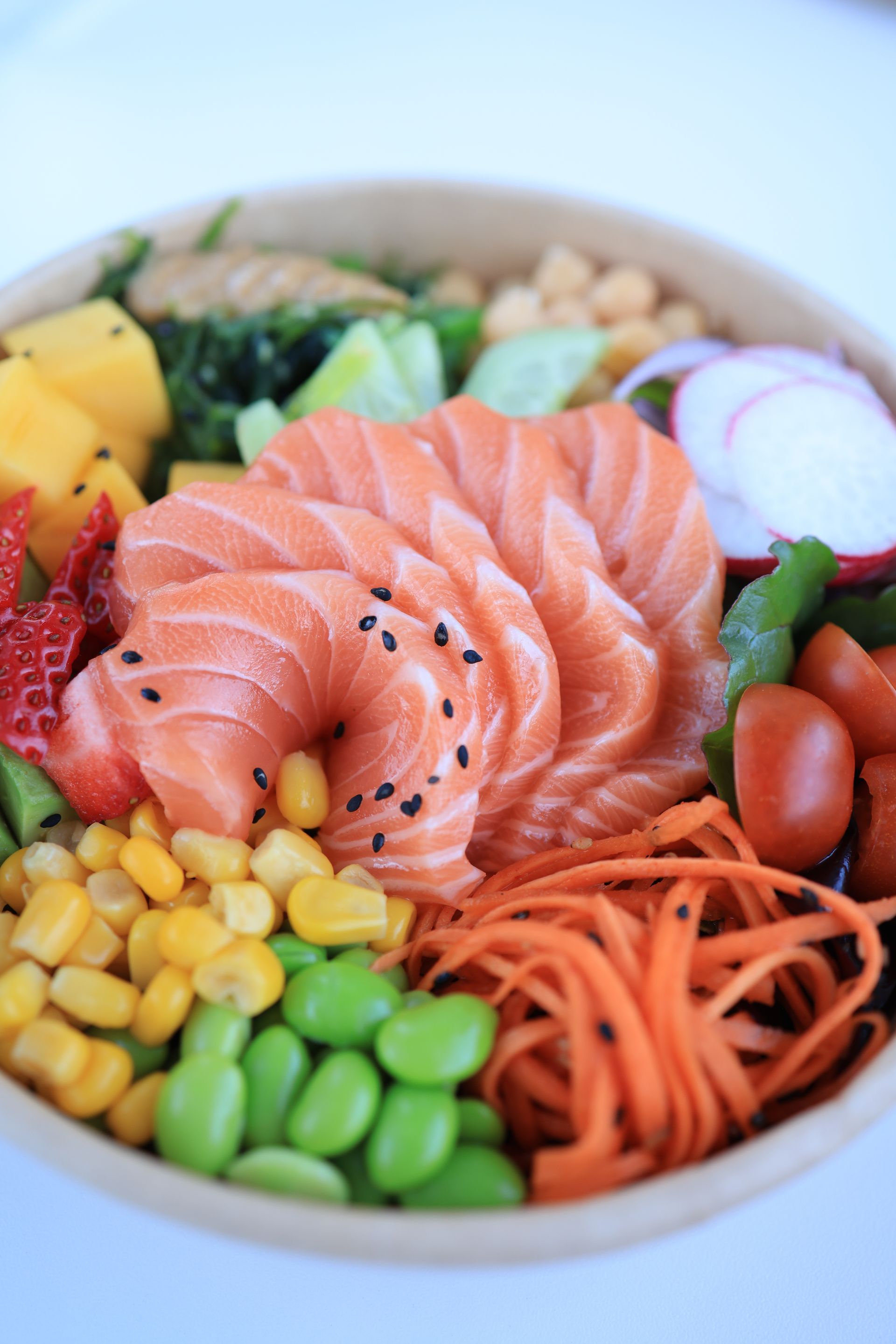
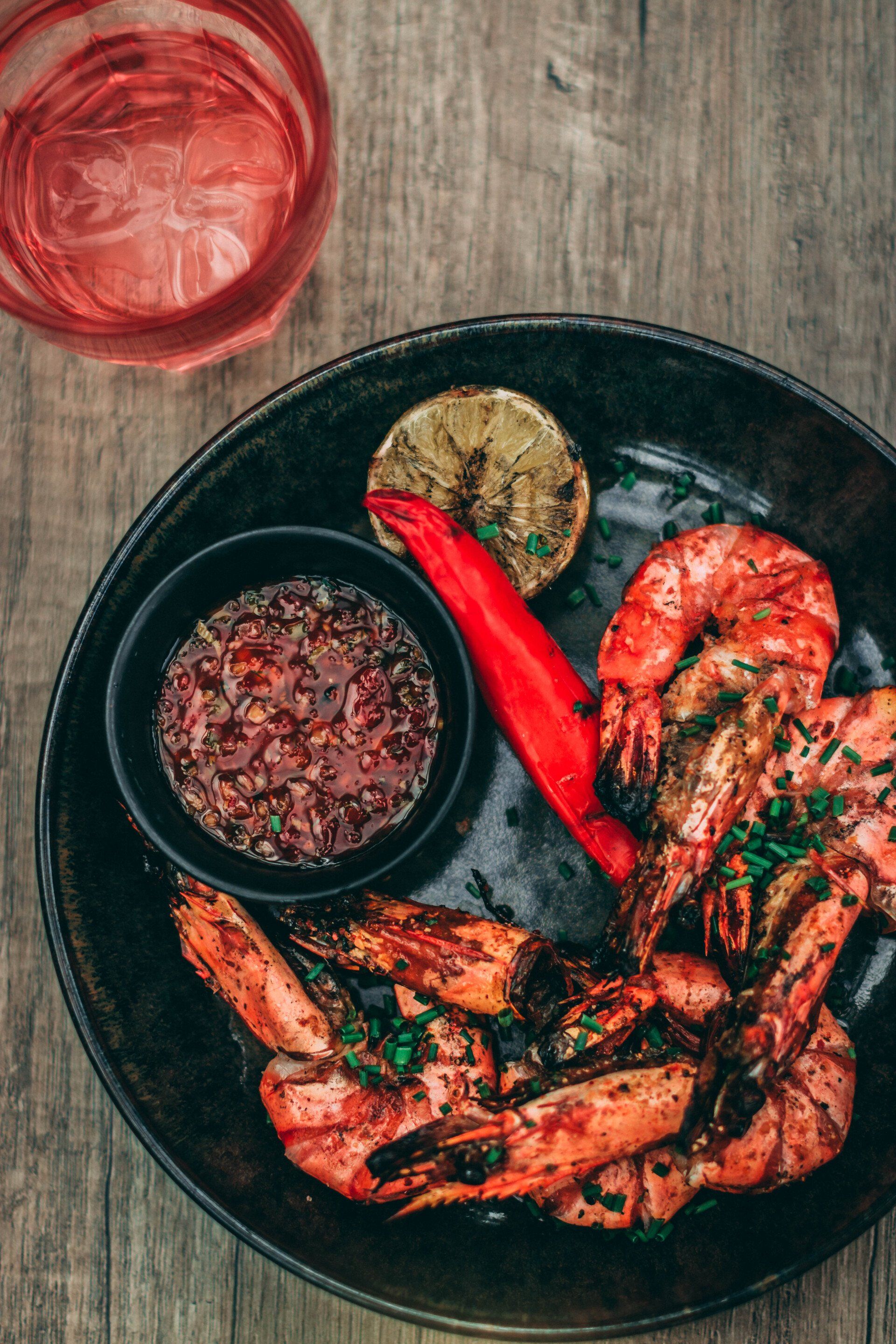
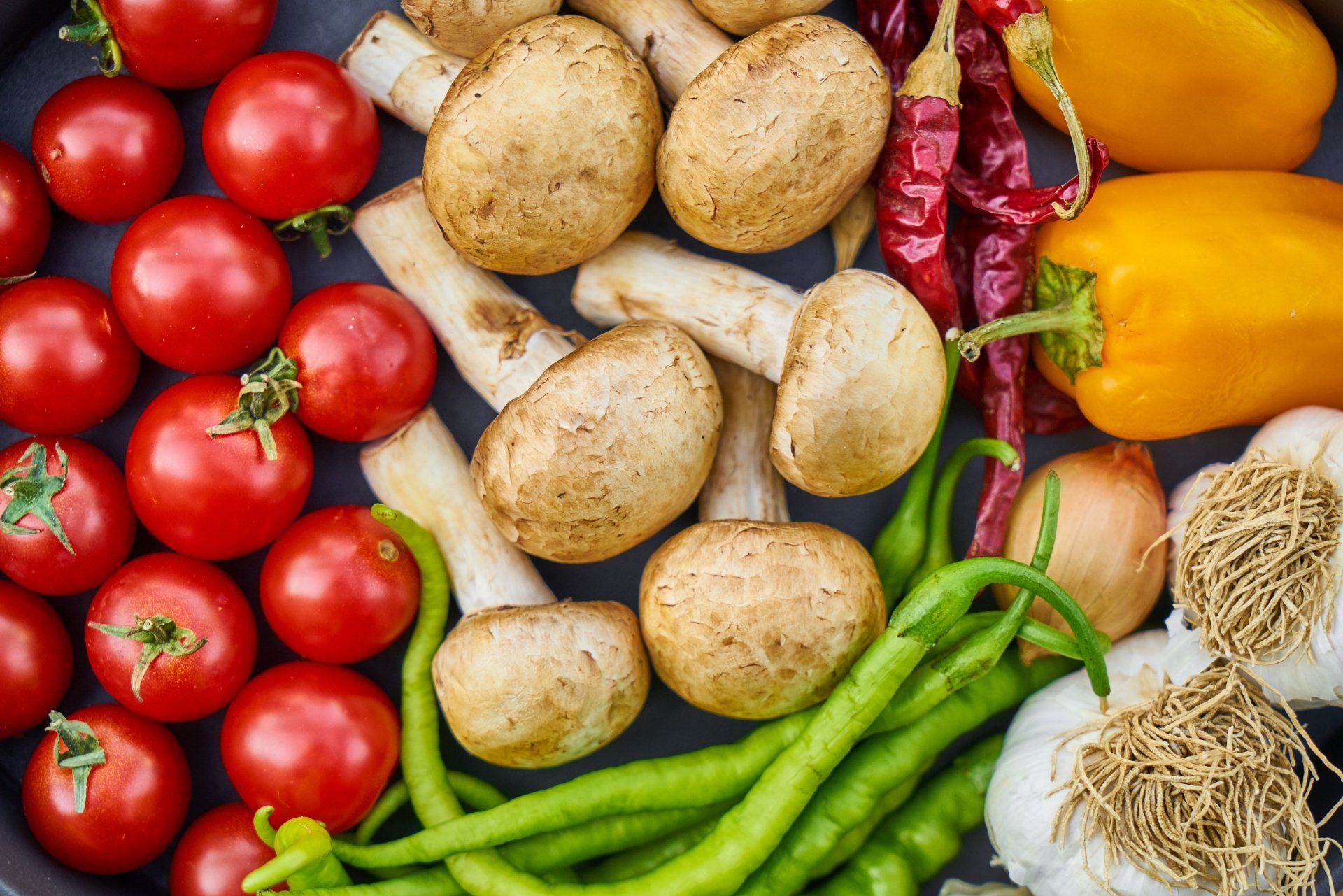
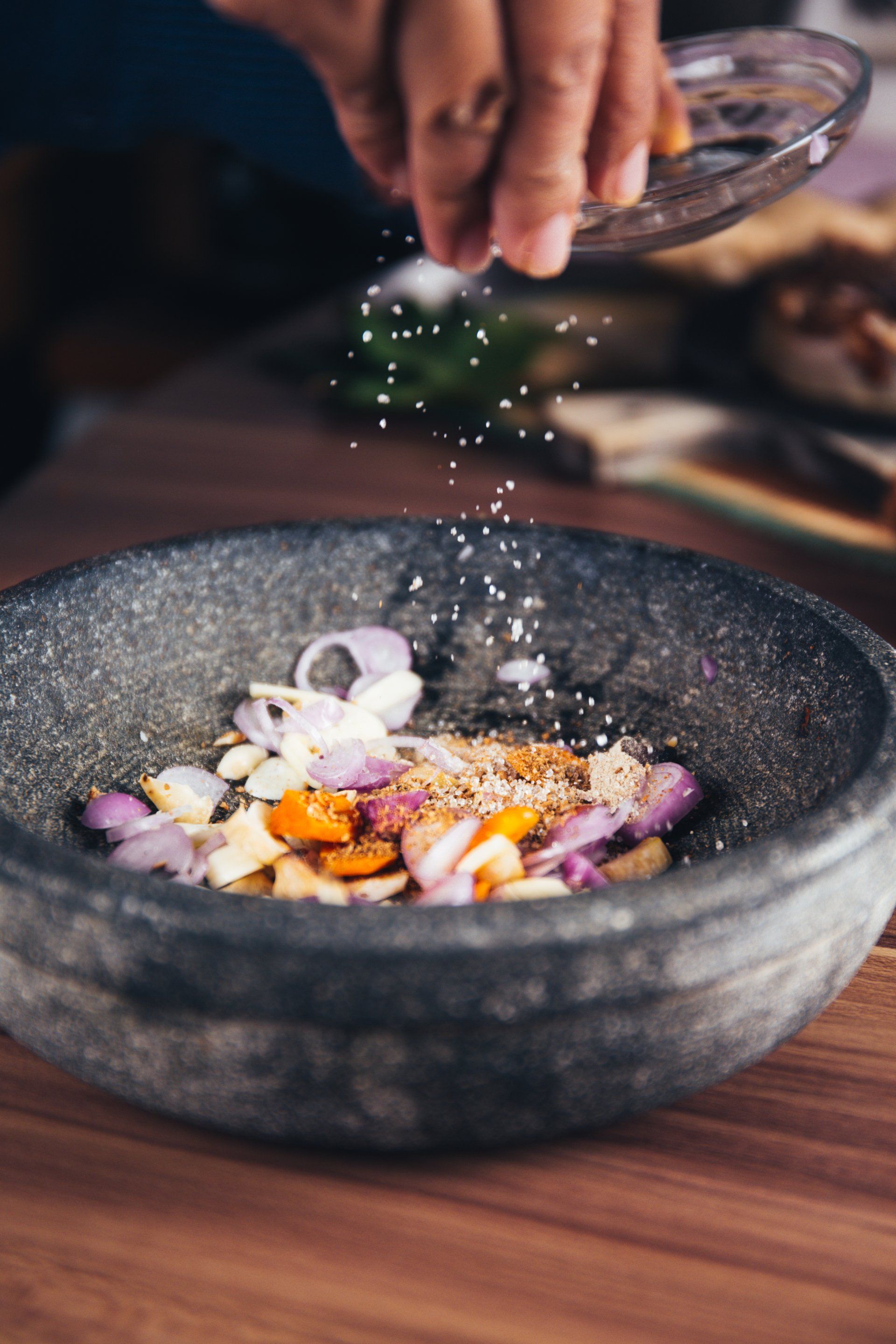
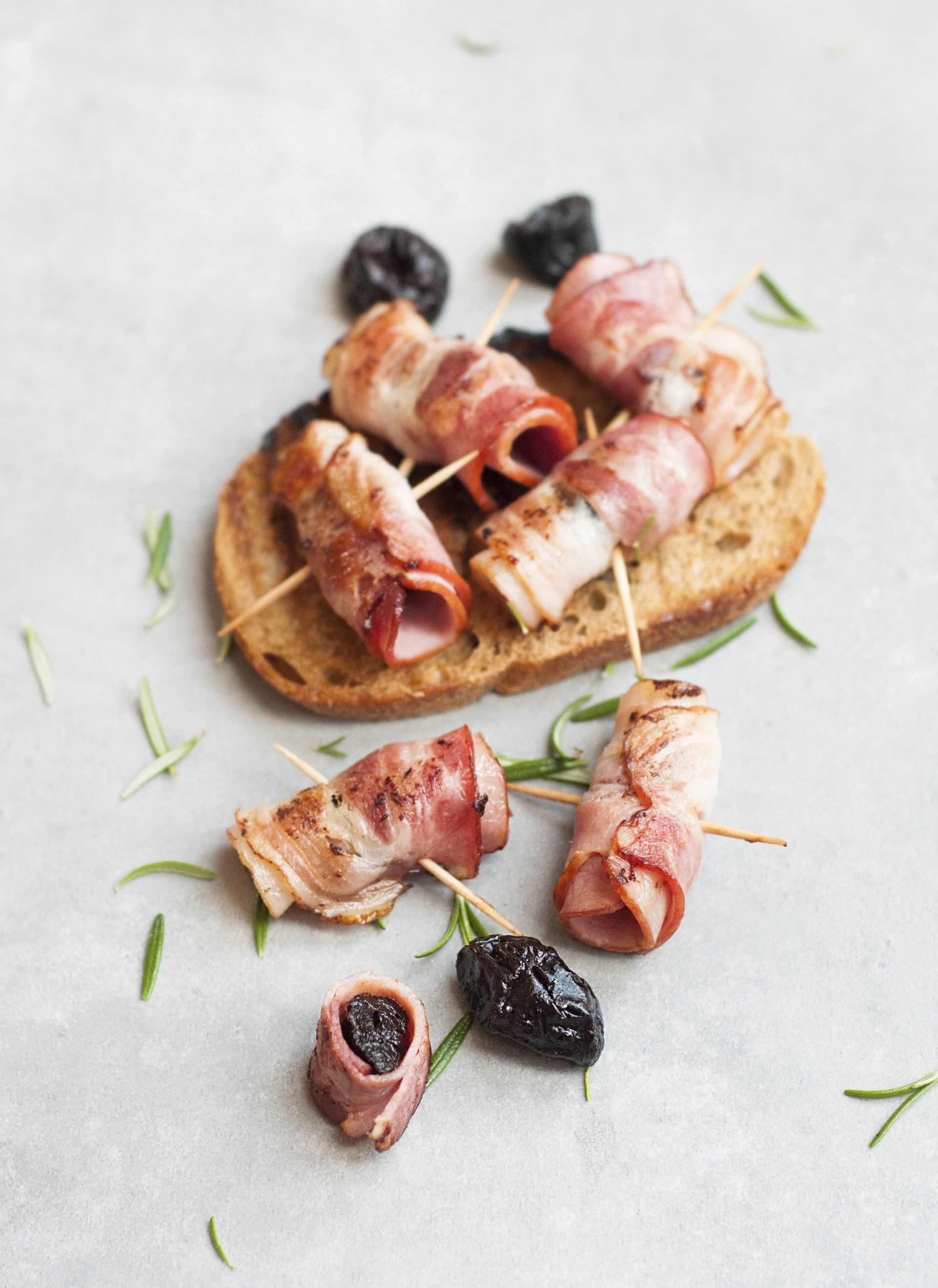